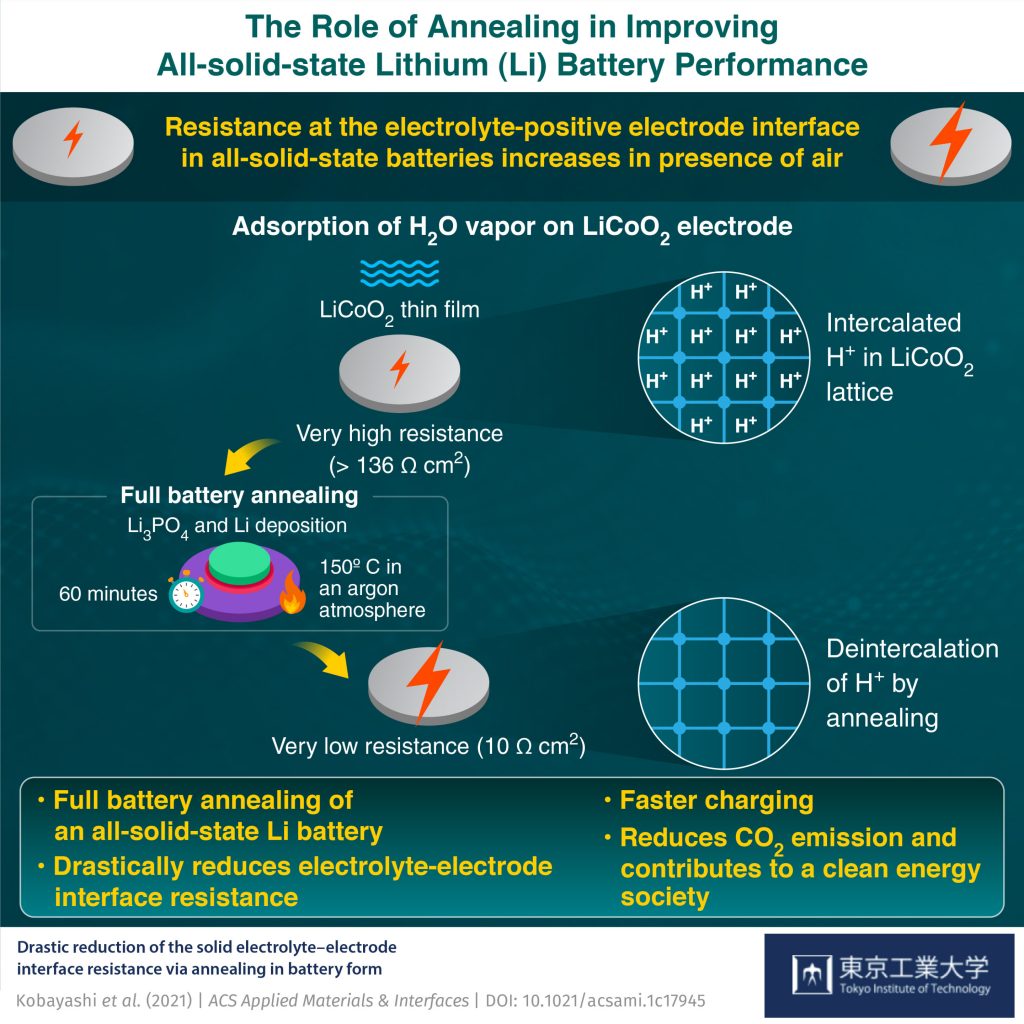
All-solid-state batteries are now one step closer to becoming the powerhouse of next-generation electronics, as researchers from Tokyo Tech, National Institute of Advanced Industrial Science and Technology (AIST), and Yamagata University introduce a strategy to restore their low electrical resistance. They also explore the underlying reduction mechanism, paving the way for a more fundamental understanding of the workings of all-solid-state lithium batteries.
All-solid-state lithium batteries have become the new craze in materials science and engineering as conventional lithium-ion batteries can no longer meet the standards for advanced technologies, such as electric vehicles, which demand high energy densities, fast charging, and long cycle lives. All-solid-state batteries, which use a solid electrolyte instead of a liquid electrolyte found in traditional batteries, not only meet these standards but are comparatively safer and more convenient as they have the possibility to charge in a short time.
However, the solid electrolyte comes with its own challenge. It turns out that the interface between the positive electrode and solid electrolyte shows a large electrical resistance whose origin is not well understood. Furthermore, the resistance increases when the electrode surface is exposed to air, degrading the battery capacity and performance. While several attempts have been made to lower the resistance, none have managed to bring it down to 10 Ω cm2 (ohm centimeter-squared), the reported interface resistance value when not exposed to air.
Now, in a recent study published in ACS Applied Materials & Interfaces, a research team led by Prof. Taro Hitosugi from Tokyo Institute of Technology (Tokyo Tech), Japan, and Shigeru Kobayashi, a doctoral student at Tokyo Tech, may have finally solved this problem. By establishing a strategy for restoring the low interface resistance as well as unraveling the mechanism underlying this reduction, the team has provided valuable insights into the manufacturing of high-performance all-solid-state batteries. The study was the result of a joint research by Tokyo Tech, AIST, and Yamagata University.
To start off, the team prepared thin film batteries comprising a lithium negative electrode, an LiCoO2 positive electrode, and an Li3PO4 solid electrolyte. Before completing the fabrication of a battery, the team exposed the LiCoO2 surface to air, nitrogen (N2), oxygen (O2), carbon dioxide (CO2), hydrogen (H2), and water vapor (H2O) for 30 minutes.
To their surprise, they found that exposure to N2, O2, CO2, and H2 did not degrade the battery performance compared to a non-exposed battery. “Only H2O vapor strongly degrades the Li3PO4-LiCoO2 interface and increases its resistance drastically to a value more than 10 times higher than that of the unexposed interface,” says Prof. Hitosugi.
The team next performed a process called “annealing,” in which the sample underwent a heat treatment at 150°C for an hour in battery form, i.e., with the negative electrode deposited. Amazingly, this reduced the resistance down to 10.3 Ω cm2, comparable to that of the unexposed battery.
By performing numerical simulations and cutting-edge measurements, the team then revealed that the reduction could be attributed to the spontaneous removal of protons from within the LiCoO2 structure during annealing.
“Our study shows that protons in the LiCoO2 structure play an important role in the recovery process. We hope that the elucidation of these interfacial microscopic processes would help widen the application potential of all-solid-state batteries,” concludes Prof. Hitosugi.