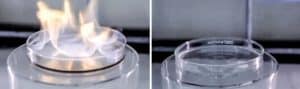
Traditional electrolyte solutions for Li-ion batteries (left) are highly flammable. The one developed at Nanotech Energy (right) doesn’t burn even when exposed to a blowtorch.
What drives entrepreneurial scientists to take an idea discovered in the lab and turn it into a business, especially in areas where other companies have failed?
The transition doesn’t happen in a puff of magic or a single eureka moment. “These companies don’t just come out of the ether from one unexpected lab development. There are many steps along the way,” says Paul V. Braun, a materials scientist at the University of Illinois Urbana-Champaign (UIUC), who cofounded Xerion Advanced Battery, where he serves as chief technology officer. The idea to launch a start-up may not sprout suddenly, but there are often decisive moments that drive the germination process.
For Xerion, which is located near Dayton, Ohio, one of those moments came when researchers discovered a valuable method for depositing battery materials on a metal current collector—an important step in making batteries. For SES, a spin-off from the Massachusetts Institute of Technology, a major advance resulted from MIT researchers figuring out how to make a safe electrolyte for batteries that feature metallic lithium electrodes. And for Nanotech Energy, which grew out of advances made at the University of California, Los Angeles, one turning point was when scientists realized that their novel form of graphene was an outstanding electrode material.
In each of these cases, the researchers recognized that their discoveries could be the start of something big. These companies have long moved past prototypes and early pilot-scale studies. They have partnered with large, well-known companies and have raised millions of dollars. If all goes well, their batteries may soon end up in electric vehicles and other types of brand-name consumer products.
Moving beyond an initial discovery requires a lot of confidence and a major investment of time, effort, and money. But that’s not enough to ensure that a company will do well. Timing is also critical. One of the keys to launching a successful start-up is anticipating an important need—such as powerful batteries to electrify transportation—long enough in advance to do the necessary R&D to win investor confidence in a company’s ability to compete in the market.
Here we explore how the story of these three companies unfolded.
XERION ADVANCED BATTERY
At UIUC, Braun’s group had been working on well-ordered porous materials in the early 2000s. The studies initially focused on depositing semiconductors in the materials’ pores to make 3D photonic crystals for light-driven microelectronics. By the end of the decade, the researchers had pivoted to metallic structures. They came up with a way to make 3D porous metals and coat them with electroactive materials, the kinds used in batteries. That finding, which Braun patented, suggested an inexpensive route to making batteries that could be charged and discharged faster than commercial lithium-ion ones.
Enter John Busbee. Busbee had completed his PhD work with Braun years earlier and had served as the nanotechnology program manager for the Air Force Research Laboratory (AFRL) at Wright-Patterson Air Force Base. In that role, he was involved in research at the early stages of nanoscience, when researchers everywhere were extolling the virtues of nanostructured materials and their endless potential for killer applications.
“There was a lot of hype in the industry back then,” Busbee says. “But the 5% that was real had so much potential. I wanted to make nanotechnology practical.” The materials advances at UIUC made by Braun’s group looked like a great start, he thought. So in 2010, Busbee cofounded Xerion, became its CEO, and set about the business of building a company—raising funds, licensing technology from UIUC, and assembling a team of researchers and financial experts to advance the battery know-how toward commercialization.
One scientific finding in particular propelled the young company’s technology forward. Xerion researchers, together with coworkers at UIUC, came up with a simple, one-step procedure for coating metal current collectors with lithium cobalt oxide, lithium manganese oxide, and related electrode materials at the heart of Li-ion batteries (Sci. Adv. 2017, DOI: 10.1126/sciadv.1602427). That method, based on electrodeposition, or electroplating, was simpler and faster and operated at lower temperature than other common deposition methods.
With additional R&D, Xerion soon had two core technologies—StructurePore, for making porous, nanostructured metal foams, and DirectPlate, for depositing electroactive battery materials. Together, they provide the company with ways to make Li-ion batteries that offer numerous performance and manufacturing advantages over standard commercial versions.
For example, the electrodes’ networks of interconnected pores and channels speed up transport of lithium ions through the battery and lower its internal resistance, boosting performance relative to batteries with nonporous electrodes. And the thin, porous electrode structure accommodates ion shuttling without the swelling and shrinking that often cracks other types of electrodes and eventually causes them to fail.
Xerion’s electroplating method provides additional advantages over existing electrode-making processes. Most battery makers start with costly, high-purity metal oxides, add carbon black to increase conductivity and an organic binder to serve as a glue, then cast the mixture as a slurry on an aluminum-foil current collector. The carbon black and binder play a role in this mixture but they don’t store charge and they add to battery weight.
Xerion uses low-cost, unrefined precursors, skips the carbon black and binder, and doesn’t deposit the electroactive battery material as a slurry. Instead, the company’s scientists dissolve lithium, cobalt, manganese, and other metal precursors in an electroplating bath. Then they switch on an electrodeposition process that forms high-purity oxides as it runs and directly plates the material on the current collector. Overall, the method lowers material costs, simplifies manufacturing, and leads to batteries with up to 20% more active battery material, which increases energy density and other performance characteristics.
“We’re using electroplating, which is a 150-year-old manufacturing technique, to make advanced batteries,” Busbee says. That approach enables the company to work directly with US mines to obtain low-purity minerals and bypass costly refinement steps. It also simplifies battery recycling because the batteries contain fewer components than traditional ones. Although Busbee is not yet prepared to share names and details, he notes that Xerion is “working with large, well-established companies in the automotive and electronics industries” and has “joint development agreements coming to realization very shortly.”
When asked about his level of optimism when he started the company, Busbee laughs. He points out that when he and the other cofounders were getting serious about licensing technology and fundraising, A123 Systems, a promising battery spin-off from MIT that had hundreds of millions of dollars in backing and some 2,500 employees, looked as if it was about to go bankrupt. (It went bankrupt in 2012.)
“People asked me ‘Why on earth would you start a battery company now?’ ” He answered—“You don’t start a company when things look good. You start them when they look bad, with the aim that when you’re ready to start manufacturing, things will be in good shape” and the market will be ready for your product. As he considers Xerion’s prospects today, Busbee says, “It seems like that plan is working out fortuitously.”
SES
SES also began its journey as A123 went bankrupt. As CEO Qichao Hu tells the story, the concepts underpinning the company’s technology were born in the late 1990s in an MIT basement lab where Hu was doing doctoral—and, later, postdoctoral— work with materials chemist Donald R. Sadoway. The work focused on batteries with metallic lithium electrodes.
The energy in standard Li-ion batteries comes from the electrochemical process that occurs as lithium ions shuttle from the Li-doped carbon anode, diffuse through a liquid electrolyte solution, and pass through a polymer separator to the metal oxide cathode. Charging drives the ions back to the anode.
In contrast, the anode in lithium-metal batteries is pure lithium metal, so those batteries pack much more lithium—and associated energy—into cells that are the same size and weight as those of their Li-ion counterparts. But Li-metal batteries are prone to forming needle-like lithium dendrites during charging that can grow from the anode, pierce the separator, and reach the cathode—sometimes short-circuiting the battery. A short circuit in a lithium-based battery can trigger a sudden release of heat, causing the organic electrolyte solution to catch fire and the battery to explode. Because of these safety concerns, rechargeable Li-metal batteries have not been commercialized despite years of research. The MIT group developed strategies for controlling dendrite growth.
In 2012, Hu launched SES (originally SolidEnergy Systems), licensed the technology developed with Sadoway from MIT, moved into A123’s recently vacated facility in Waltham, Massachusetts, and began its own R&D program. Initially SES was working on Li-metal batteries with a solid electrolyte to prevent dendrite growth. But that electrolyte caused manufacturing difficulties, Hu says. The company soon discovered a novel solvent-in-salt electrolyte—a type of ultraconcentrated ionic solution—that curtailed dendrite growth and proved compatible with standard battery manufacturing practices. Hu refers to cells made with this electrolyte as hybrid Li-metal cells. Hu says SES eventually dropped the MIT license but adds that “the fundamental studies done at MIT remain at the core of our Li-metal development today.”
In a virtual conference in November 2021, Hu presented data on SES’s hybrid Li-metal batteries that showed exceptional energy density—the amount of energy batteries can deliver on a per-weight basis—over a wide range of temperatures and discharge rates. Such performance under various situations is critical for electric vehicles, he said, because they’re used in hot and cold climates to drive slowly as well as accelerate rapidly. He noted that the data came from independent testing labs.
At the same event, Hu unveiled Apollo, which he described as “the largest Li-metal battery the world has ever seen.” He noted that the battery, which is more than 25 times as large as a typical mobile phone battery, weighs less than 1 kg and can deliver about 107 A h of charge over a wide range of discharge rates—record-setting values for this type of battery. According to Hu, SES is now working with a number of automobile makers to commercialize its batteries and is building a large production facility in Shanghai that’s scheduled for completion in 2023.
Hu isn’t the only one impressed with SES batteries. Shirley Meng, a Li-metal battery expert at the University of Chicago, notes that the temperature range over which the company’s batteries operate and the reported discharge rate capability exceed expectations. “The performance is extremely impressive,” she adds.
And Kent Helfrich, General Motors’ vice president of global R&D and chief technology officer, who also spoke at the 2021 virtual event, said SES’s Li-metal technology delivers in key areas, including battery cost, driving range, charging time, and manufacturability. “We think there’s a great future in front of us,” he said.
NANOTECH ENERGY
The story of UCLA-based start-up Nanotech Energy unfolded somewhat differently than those of Xerion and SES. The company did not evolve from a single puff of magic, per se, but the idea underpinning its main technology sort of did.
Maher El-Kady, a PhD student working with materials chemist Richard B. Kaner, was studying ways to use flashes of light to prepare graphene from graphite oxide, a common and inexpensive starting material for making this form of carbon. El-Kady, a member of C&EN’s Talented 12 class of 2022, found that light from a laser or camera flash instantly converted the precursor to graphene. Sheets of graphite oxide (sometimes called graphene oxide) normally stack neatly, like a thin ream of printer paper. But when El-Kady analyzed the graphene sheets produced with the light-flash method, he found that they were crumpled in a way that formed a porous 3D network.
Further analysis indicated that the flash triggers photoreactions that deoxygenate the starting material and generate heat. The process liberates gas—mainly carbon dioxide—which forces its way through the sheets, spontaneously crumpling them and forming an open 3D structure. The finding was unexpected, El-Kady says, because other methods for making graphene from graphite oxide form flakes with tightly stacked sheets. He then studied the material’s reduction-oxidation, or redox, properties using a standard electrochemical method for measuring charge transfer and discussed the results with Kaner.
“It was amazing,” Kaner recalls. El-Kady had discovered that the rate of charge transfer in the graphene made with a flash of light was 100 times as fast as that in graphite, the standard electrode material used in Li-ion batteries. “At that point, it became obvious that we should be using this material for energy storage,” Kaner says. Not only was the material an excellent electrical conductor, but its open internal structure led to intimate contact with charge-carrying electrolyte solutions key to the performance of batteries and supercapacitors. Supercapacitors are devices that rapidly store and discharge electrical energy.
The team quickly figured out how to use a low-power laser and the crumpled graphene to form intricate patterns of miniature supercapacitors (Science 2012, DOI: 10.1126/science.1216744). That work sparked interest from several investors, Kaner says, and eventually led to the founding of Nanotech Energy, where El-Kady serves at chief technology officer and Kaner chairs the scientific advisory board.
Nanotech Energy recently developed ultrasafe Li-ion batteries that don’t burst into flames when punctured or heated to high temperatures. The batteries, which have been evaluated by manufacturers of electric cars, are made with the company’s graphene, a heat-tolerant film that separates the electrodes, and a novel electrolyte solution that doesn’t ignite even when exposed to a blowtorch. The company plans to start producing the batteries in volume at a facility in Reno, Nevada, that’s scheduled to open later this year.
In a video statement about Nanotech’s batteries, Andreas Hintennach, head of battery research at Mercedes-Benz, says there’s usually a trade-off between battery safety and performance. With Nanotech Energy, however, “we have extremely safe chemistry that provides high performance now [and] we are very pleased about that.”
As with the researchers at Xerion and SES, scientists at Nanotech Energy toiled for years to move a laboratory development to a commercial product, with no guarantee of success. The people at these three companies were driven by confidence in a scientific discovery and a desire to make a difference in energy technology in what could lead to a financial windfall.
“We knew it was going to be hard when we started,” but that’s to be expected, Xerion’s Busbee says. “It’s difficult to change the world. If it was easy, someone would have done it already.”