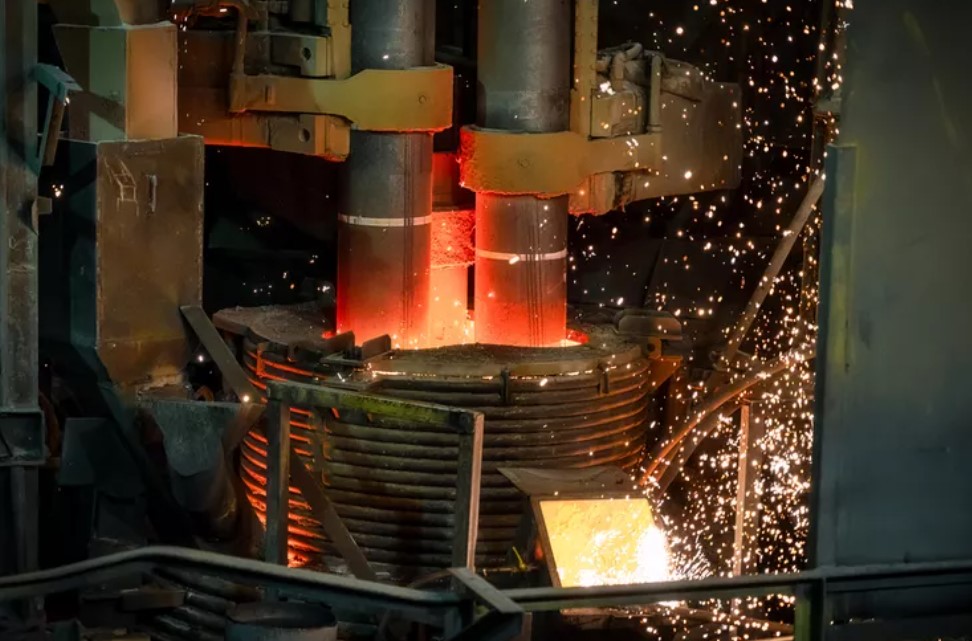
You can reduce the emissions from the cooking of calcium carbonate, but you can’t do anything about the chemistry. This is the fundamental reason that we have called concrete the most destructive material on earth and recently complained about concrete icebergs.
The Cambridge Electric Cement changes the equation. According to the press release, Dunant noticed that “used” cement separated from recycled concrete was virtually identical to the lime flux that is used to remove impurities from steel in both electric arc and basic oxygen furnaces, and which floats on top of molten steel to protect it from oxidizing. It ends up as slag, usually considered a waste product but that is full of calcium oxide—a key ingredient in the clinker used to make cement. The Cambridge team ground up the slag into a powder and found that it “is virtually identical to the clinker which is the basis of new Portland cement.”
In the Cambridge process, you take apart that reinforced concrete building and send the reinforcing steel to an electric arc furnace for recycling. You separate the aggregate from the cement and use that cement to replace the lime flux in the electric arc furnace, resulting in “novel slag” which replaces the clinker in the Cambridge Electric Cement.This is then put back together with the recycled aggregate to make new concrete and the recycled reinforcing bars to make a new building. You have basically recycled the old structure into a new one. If that electric furnace is powered by clean energy, then the entire process produces almost no direct carbon emissions. It is truly what they call “a virtuous recycling loop.”
Allwood says, “If Cambridge Electric Cement lives up to the promise it has shown in early laboratory trials, it could be a turning point in the journey to a safe future climate. Combining steel and cement recycling in a single process powered by renewable electricity, this could secure the supply of the basic materials of construction to support the infrastructure of a zero emissions world and to enable economic development where it is most needed.”
This could change the emissions picture for both the concrete and steel industries. Making lime for the steel industry produces a lot of CO2; as in making cement, it involves cooking limestone—calcium carbonate—and has the same issue of chemistry, driving off 900 kilograms of CO2 for every metric ton produced before you even account for the fossil fuels needed to heat it, which approximately doubles the footprint. According to the Multidisciplinary Digital Publishing Institute (MDPI), about 40% of lime produced goes to the steel industry, between 140 and 160 million metric tons per year. If the lime is replaced by the Cambridge process, that is a huge carbon saving right there, before you even get to the replacing of Portland cement in the concrete. There is going to be a big problem of scale; there are probably not enough buildings being demolished and the steel industry doesn’t generate nearly enough slag to replace more than a fraction of the conventional cement industry. Allwood confirmed to Treehugger: “Roughly speaking, you’re right that total CEC [Cambridge Electric Cement] production would be much less than current cement demand, although CEC produces clinker which is then ‘padded’ out with gypsum and supplementary cementitious materials to form cement—so the volume of cement is greater than the volume of slag. However, the material efficiency strategies that have been the core of our work for the past 15 years suggest that we could build with much less cement than we use today.” Dr. Cyrille Dunant also told Treehugger: “although the volumes of steel are not going to change very much going forward, the amount of cement we need is: on the basis of current demand, the slow down in population growth implies we’ll need only about 50-60 percent of today’s needs. So in effect, blending, which doubles the amount of product, plus population which halves demand, plus material efficiency, which halves it again suggests CEC could cover all future cement needs in 2050 with a margin.” These are very good points. When you look at the concrete industry’s road map to net-zero carbon, they note there could be significant savings through design and reductions in the use of cement. The UK Fires group “aims to enable a rapid transition to zero emissions based on using today’s technologies differently, rather than waiting for the new energy technologies of hydrogen and carbon storage,” two technologies that the conventional concrete industry is looking at to reduce their carbon footprint, to get around the “chemical fact of life” that is the manufacture of cement. Cambridge Electric Cement might well be an elegant way around the problem.