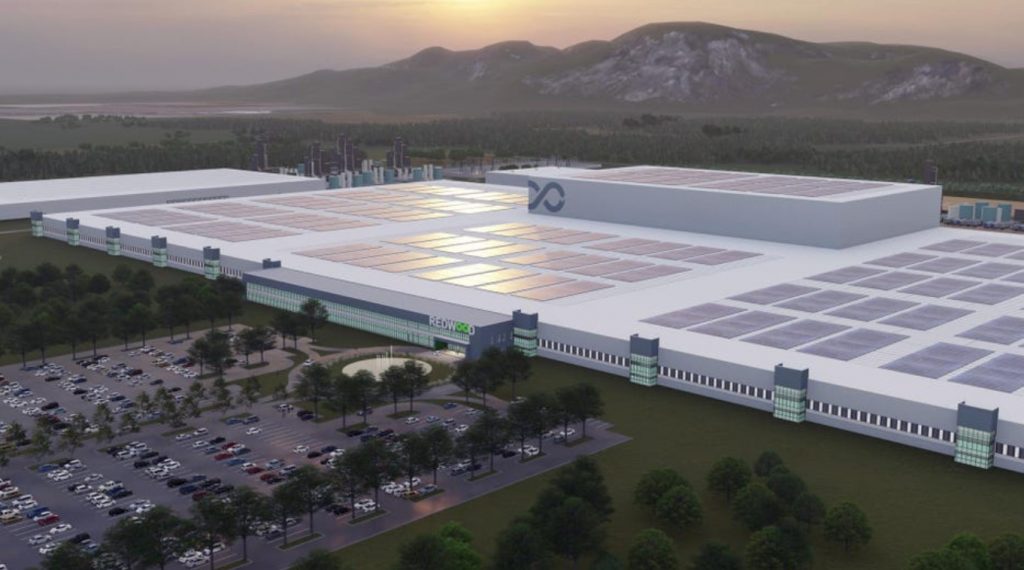
Panasonic, Tesla’s main battery partner since its earliest days, plans to use recycled materials supplied by a startup led by the electric-car maker’s former tech chief to produce lithium-ion cells in a more sustainable, “closed loop” fashion.
Redwood Materials, which already collects and recycles scrap and used battery components from Panasonic, is to begin supplying it with copper foil this year for use in making new lithium-ion cells at Tesla’s Gigafactory in Sparks, Nevada, the electronics company said Tuesday during its CES presentation. Reusing scraps and old batteries can help ensure Panasonic meets a goal of sustainable production as output grows throughout the 2020s, said Allan Swan, president of Panasonic Energy North America.
“Redwood is creating a circular supply chain for electric vehicles and clean energy products here in the United States, making them more sustainable and driving down the cost of batteries,” he said in a video presentation. “By the end of this year we expect to include Redwood’s copper foil produced from recycled materials back into our new battery production.”
Founded by JB Straubel, Tesla’s longtime chief technology officer and a cofounder of the EV company, Redwood is moving quickly to become a leading supplier of recycled metals and materials that it’s recovering from used batteries, battery scrap and electronics. Based in Carson City, Nevada, near the Gigafactory, the company has raised about $800 million to expand its recycling business as demand for EV batteries–and the costly commodities needed to make them–grows.
Redwood said Panasonic’s use of copper foil from recovered material will be the first such closed-loop battery production process–in which batteries are recycled, remanufactured and returned to the same factory.
In September 2021, closely held Redwood said it would invest more than $1 billion to construct $1 a large U.S. plant to make materials needed for EV batteries by 2025, though it hasn’t announced the location yet.
During his time at Tesla, Straubel was instrumental in overseeing the design of the carmaker’s battery pack and motors, beginning with the 2008 Roadster. He also helped set up and run the massive Gigafactory, the biggest U.S. battery plant. He left Tesla in late 2019.
Currently, Panasoninc produces about 2 billion battery cells a year at the Tesla facility.
“And as much as we’ve scaled up production, the biggest opportunity lies in front of us,” Swan said. “We’re looking at a five times growth over the next decade, as more and more vehicles go electric.”