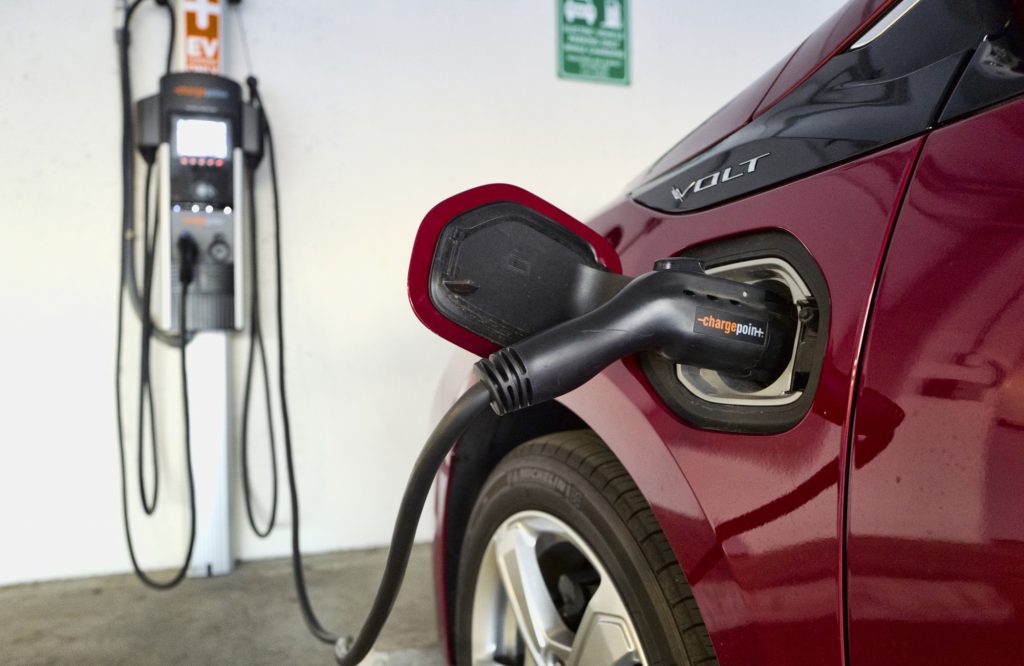
General Motors is accelerating its shift away from China and other foreign sources for the key raw materials and components needed for the millions of battery-electric vehicles it plans to roll out over the coming decade.
GM announced the latest of more than a dozen deals Thursday, saying it will purchase rare earth metals from the only remaining commercial mine in the U.S., while two new plants will provide the high-power magnets needed for its electric vehicle motors. Currently, finished magnets and raw materials, such as neodymium, are sourced largely from China.
“Our intent is we will have a fully resilient, sustainable, scalable and cost-competitive supply chain for the entire value chain through a North American-focused supply chain to support all of our EV production,” said Shilpan Amin, GM’s vice president of global product development, purchasing and supply chain.
The first “strategic collaboration” announced Thursday pairs GM and MP Materials, the California-based company that operates the only commercial U.S. rare earth mine, in Mountain Pass. MP, which will provide raw and processed minerals, will also set up a factory in Fort Worth, Texas, to produce enough magnets for up to 500,000 electric motors annually.
Separately, GM said it is finalizing the details of an agreement with Germany’s Vacuumschmelze, or VAC, to supply rare earth minerals, as well as the finished magnets. VAC will also set up a U.S. magnet factory for GM, with the location to be announced next year.
“VAC’s deep magnetic materials knowledge and extensive e-mobility technology expertise, in partnership with GM, will enable a cleaner global future for our communities,” Erik Eschen, VAC’s CEO, said in a statement.
Amin said the two deals are expected to create “hundreds” of jobs and provide enough magnets for all the motors GM will need going forward.
Previous deals have laid out plans for GM to source raw minerals to finished components from suppliers in the U.S. and Canada. That’s a critical move, said analyst Stephanie Brinley of IHS Markit. It would not only reduce dependence on potentially unreliable trade partners, like China, but also minimize the risk of supply chain disruptions. Shortages of foreign-made semiconductors have crippled U.S. automotive manufacturing this year, resulting in empty dealer lots and billions of dollars in lost industry revenues.
The auto industry, on the whole, is shifting from internal combustion to battery technology. GM has one of the industry’s most aggressive transition plans. CEO Mary Barra this year raised GM’s planned spending on electrified and autonomous vehicles from the target of $20 billion announced last year to a new goal of $35 billion. It is expected to bring at least 30 pure battery-electric vehicles to market by 2025. It plans to abandon gas and diesel vehicles entirely by 2035.
GM’s first long-range battery-electric vehicle, the Chevrolet Bolt, came to market in 2016. It is just launching the GMC Hummer EV, with the Cadillac Lyriq to follow in mid-2022. The Hummer pickup and the Lyriq SUV will use an entirely new Ultium platform and batteries expected to yield longer range, faster charging and lower costs.
One of the biggest concerns for automakers is ensuring a supply of raw materials like neodymium, cobalt, nickel and lithium. Lithium could prove increasingly difficult to find, some experts fear, as production of batteries ramps up. GM hopes to cover future needs through another joint venture announced this year. The project will filter lithium, a lightweight metal, out of water drawn from California’s Salton Sea Geothermal Field.
GM has announced four U.S. battery plants so far. The first, in Lordstown, Ohio, is powering up the new Hummer pickup.
“Fundamentally, our strategy is to control our own destiny,” Amin said.